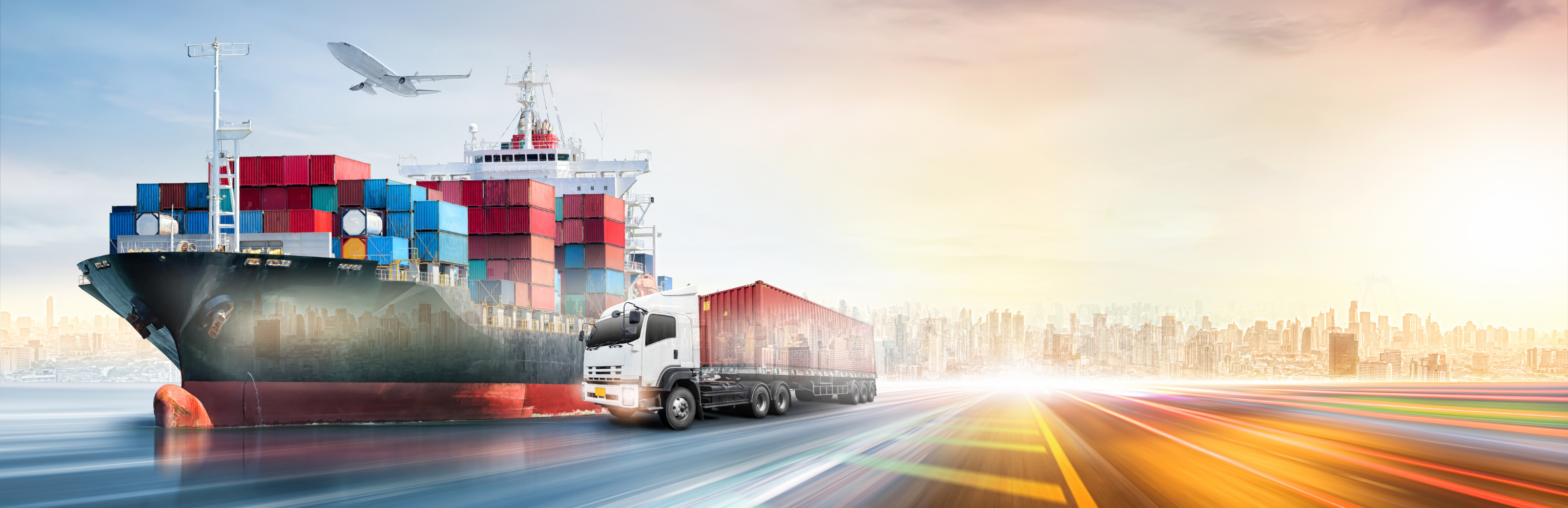
Automotive supply chains have become extremely complex and vulnerable but change is coming.
As featured in Australasian Automotive June 2023.
We’ve heard a lot about supply chains in recent times. Automotive supply chains are some of the most complex in the world because of the wide range of materials needed to make the broad range of vehicle components required. What’s more, the range of techniques utilised in vehicle construction is impressive and includes cutting, bending, pressing, casting, welding, moulding and more. It’s a complex business.
‘Tier 1 supplier’ is a common term generally taken to mean a company that supplies directly to a vehicle manufacturer, or OEM. That’s correct but the definition can be expanded. A Tier 1 supplier supplies complete components that are directly incorporated on the production line. An entertainment unit is a complete component, as is a seat, a transmission, a headlight, a braking system, and so on. Panels and engines might come from Tier 1 suppliers or OEMs may produce them in-house. Although Tier 1 is the most commonly heard term, there are three supplier tiers.
Tier 2 companies supply Tier 1 companies with the separate parts needed to manufacture a complete component, as described above. For instance, an entertainment unit has many sub-components such as a touch-screen, electronic components, circuit boards, plastic parts like knobs, buttons and enclosures. A Tier 2 supplier supplies these to Tier 1 suppliers for assembly into a complete entertainment unit. However, the complexity of modern components means a Tier 1 supplier might receive parts from many Tier 2 suppliers. It gets complex. Bosch, for instance, is a Tier 1 supplier and it’s not difficult to imagine the massive number of Tier 2 suppliers it draws upon for its huge range of automotive components.
Tier 3 suppliers deal mainly with the raw materials used to make the parts produced by Tier 2 suppliers. So, metals, plastics, rubber, glass, and more. The automotive supply chain is the vast, interconnected network of all these suppliers and it’s completely global. Sometimes the term logistics is used to mean supply chain but that’s incorrect. Logistics is a part, a big part, of the supply chain that handles the movement of components within this global network.
OEMs have very close relationships with their Tier 1 suppliers. Indeed, sometimes Tier 1 supplier factories are co-located with the OEMs they serve. In a number of cases the factories are conjoined. Further, some Tier 1 suppliers are owned, or partially owned, by OEMs. Aisin is the world’s sixth largest Tier 1 supplier and DENSO is the second largest. These were both started in 1949 by Toyota, which retains holdings of about 33 per cent in each company.
Toyota’s relationship with its Tier 1 suppliers is intimately linked to the processes that have defined automotive manufacturing over past decades. In the early 1950s Eiji Toyota visited the gigantic Ford Rouge River plant in Michigan. While it was impressive, Toyota knew it wasn’t a practical approach for Japan at that time. It required too much stock on hand and that called for large capital investment. Unfortunately, capital was in short supply in post-war Japan.
Toyota also visited a supermarket, which was something Japan didn’t have at that stage. Reportedly, he was interested in the way customers could simply choose what they wanted from a shelf and impressed with the idea such stock could promptly be replaced on the shelf. The potential of maintaining constant stock levels in this way inspired the idea of just-in-time manufacturing. This became, and has remained, the mainstay of OEM manufacturing. Indeed, the mobile autonomous trolley system that delivers parts to the production line at the Mercedes-Benz S-Class factory is referred to by the company as a ‘shopping basket’.
Because times were so tight in post-war Japan, the Toyota company found ways of doing more with less. This was and is the basis of Toyota’s Kaizen approach to manufacturing and the efficiencies bound up within it. Essentially, Kaizen is the process of, and attitude to, iterative and constant improvements in products and processes. It is the very opposite of the notion expressed by the excuse: “We’ve always done things that way”.
Toyota is responsible for a number of other manufacturing innovations adopted by established OEMs. Kanban is one of the most widely cited and was also born of 1940s shortages. It consists of visualising the production process and representing it physically. Originally, this was done with card displays but now processes and resources are represented digitally. The characteristics of each process are defined and steps are taken to ensure the processes represented match those defined on the Kanban board.
The modern principle of Lean Manufacturing was also developed (though not invented) at Toyota. Basically, it’s all about waste reduction in all manufacturing processes and holding minimum amounts of stock. There are many other oft heard manufacturing philosophies like Six Sigma, 5S, and TOC.
The above summaries are general. The detail of these systems is deep and complex, however they are all united by at least one thing (and, actually, a good many others) and that is the relationships between OEMs and their tiered supply networks. These days, these relationships are entirely dependent on global supply chains. It’s a small world.
Globalisation and extended world trade have been a boon to all industries, automotive manufacturing included. It’s the reason for the cheap products we enjoy and the massive profits we subsidise. It’s built upon the stable global supply chains we’ve enjoyed for decades. However, things are changing and such changes are highlighted by two major world events.
In 2019 the COVID-19 assault on production and trade around the world began, leading to the shortages and restrictions we all remember so clearly. The shortage of automotive microchips received the most publicity but there were other disruptions to supply chains and we’re still recovering from them. Then, in March 2021, the gigantic Ever Given container ship became wedged across the Suez Canal, revealing a major choke point in all global supply chains, including automotive.
It was already known this section of the Suez Canal was a potential disruption and there were, and are, plans to widen it to allow transit in both directions. However, because passage is only possible in one direction at the moment, ships must gather in staging areas before travelling through in convoys in one direction. That the possibility of disruption bound up in this procedure wasn’t part of supply chain risk management is an example of the consequences of adhering too strictly to the manufacturing principles outlined above, like just-in-time parts supply. Now, OEMs adjust their stock levels and those of their Tier 1 suppliers to compensate for such disruptions. But it’s not as simple as that.
The above mentioned manufacturing paradigms were successful because they imparted benefits. Moving away from them to a degree by building buffers has resulted in stock sitting in expensive storage and losing value. Another consequence of stock shortages due to supply chain disruption has been feature reductions on various models. These are less than ideal short term solutions. There are other challenges to supply chains looming.
In 2022, global accounting giant KPMG published a report on the vulnerability of global automotive supply chains. It says that expectations of protectionist sentiments and restrictive trade policies are likely to increase in the coming years. Trade difficulties with China are obvious and even companies that haven’t been directly effected yet are making moves to insure themselves against disruptions in relations with this giant.
For instance, Tesla uses lithium from Australia, Peru, Argentina, Bolivia and Chile. The last three are known as the lithium triangle. So, that’s a pretty diverse supply chain. However, most of that lithium is shipped to China for processing and from there to Tesla and other OEMs. Indeed China processes 75 per cent of the world’s lithium.
Tesla signed a five-year deal with one of the major Chinese lithium processors in 2020. However, it also recently announced its plan to extract lithium from clays in Nevada and process it in the US. This is another sign of the trend for on-shoring and re-shoring US industries to build buffers against supply chain vulnerabilities. Musk encouraged investors to get into the lithium processing business saying, “You can’t lose, it’s a licence to print money”. There’s a strong lesson in that for Australia.
The KPMG report suggested a couple of the ways forward in supply chain risk management is for companies to adopt the practice of regionalisation of supplies where possible and of using multi-source suppliers generally. Tesla’s strategy ticks both boxes. Also mentioned is the need to comply with ESG (Environmental, Social and Governance) policies and regulations.
Another thing that’s as important to supply chains, as it is to virtually every other industry, is AI and data analysis. As automotive supply chains diversify and link with more suppliers to increase supply redundancy they are becoming more complex and difficult to assess and manage. Analysis by AI has become essential. However, this is not a surprise.
Every company of any size, and virtually all companies connected with automotive supply chains, are across AI analytical technology, the necessity for it and the benefits it brings. AI and data analysis is as important as Kaizen, Kanban and Lean Manufacturing combined. In fact, the insights needed for future success in supply chain and manufacturing will come from AI algorithms and data analysis rather than the implementation of human inspired programs. Times have changed.
The elephant in the automotive supply chain room is China. In fact, China is so heavily intertwined in all global manufacturing that armed conflict with the PLAN (People’s Liberation Army Navy) would be disastrous for global manufacturing and supply chains. So, will there be a conflict over Taiwan?
China’s navy is larger than that of the US. For perspective, we should point out it doesn’t have the technical capacity of the US or Japanese fleets and global strategist Peter Zeihan points out much of the PLA naval force isn’t blue water capable; it’s restricted to shorter range missions. Still, we don’t see much comfort in that because Taiwan is only a couple of hundred kilometres off the Chinese coast.
The Chinese military has also grown at an enormous rate. For example, the US has seven major shipyards. China has 19 and one of them has a production capacity equal to all seven US facilities. Other branches of its military are also expanding. Originally, it had 20,000 marines but plans to expand that force to 100,000. Marines are used primarily for invasions.
Still, according to the very perceptive Zeihan, and others, China has some vulnerabilities. It’s a huge importer of energy, food and raw materials. It’s economy is also entirely reliant on exports; much of its population is poor and can’t afford its output, so it’s not economically self-sufficient. Consequently, sanctions of the same magnitude as those levied against Russia would cripple the country. The trouble is, such sanctions would also have devastating effects on all global supply chains, including automotive. And decoupling Western manufacturing from China would be extremely difficult, although we may be seeing the first signs of this. At best, it’s an extremely volatile scenario.
Really, in the end, why would Australia care about the automotive supply chain given we no longer manufacture passenger cars? Well, we still buy vehicles and they have to be manufactured and they also have to be shipped here. This brings up the automotive value chain, which is the entire chain of automotive activity from design, through all levels of manufacturing, transport of finished vehicles and sales. Any disruption along that chain, particularly in the supply chain, can break the chain. Australia needs to plan for a role in a revised, more robust but more regionalised automotive supply chain. A good start would be to process the things we dig up, particularly our own lithium.
As featured in Australasian Automotive June 2023.